Recommended Blogs
Intelligent Automation in QSR: From Order to Delivery
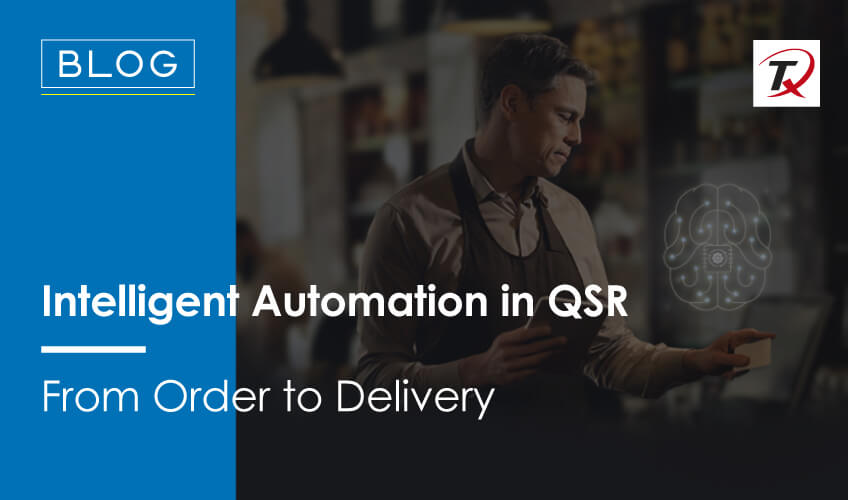
Technological advancements have been upscaling various industries recently, and the quick-service restaurant sector is no exception. Intelligent automation is reshaping how users experience the QSR world from order to delivery process. Millennials and GenZs demand tech-driven dining experiences, and technologies like AI and automation play a big role. Major chains like McDonald’s, KFC, and Chipotle use these technologies to optimize customer experiences and processes. Fast-food restaurants, already optimized for drive-thru and takeouts, reduced foot traffic by 50-60% by focusing on online ordering and delivery services.
With brands heavily investing in technologies like AI and automation to enhance customer interaction, such as self-ordering kiosks and kitchen display systems, the QSR industry is witnessing a transformation focused on efficiency and customer satisfaction. In addition to technical upgrades, the industry is also adapting to offering better alternatives for diners with specific preferences and dietary needs.
What is Intelligent Automation?
Intelligent automation, or cognitive automation, refers to using automation technologies like AI, BPM, and RPA to streamline and upscale decision-making across organizations. Utilizing various applications allows businesses to simplify processes, free up resources, and enhance operational efficiencies. For example, in the fast-food industry, AI/ML and robotics help transform how QSRs function, from order placement to delivery. Let’s take a look at the three components of intelligent process automation.
Artificial Intelligence (AI)
AI is the brain behind intelligent automation. In QSRs, AI is critical in various applications, from analyzing customer data to enhancing personalized experiences to facilitating chatbots for better support services. AI algorithms can predict user preferences, helping restaurants create menus and marketing strategies more effectively. They also help forecast demand to optimize inventory management and reduce food wastage.
Business Process Management (BPM)
BPM improves and optimizes business processes. QSRs involve streamlining processes, such as order processing, kitchen management, customer service, etc., to reduce operational costs and improve efficiency. BPM tools can map all QSR processes, identify bottlenecks, and devise strategies to optimize workflow, ensure consistent service quality, and upscale productivity.
Robotic Process Automation (RPA)
This component involves using software bots or robots to automate routine and repetitive tasks, such as order entry, billing, customer interactions, and some aspects of food preparation and packaging. It speeds up operations and reduces human error, increasing service accuracy and consistency.
Role of Intelligent Process Automation in the QSR Industry
QSRs, or fast-food restaurants, set an example for the rest of the commercial world in surviving uncertain times during the pandemic. Thanks to intelligent process automation (IPA) and other digital transformation technologies, QSR business owners found various ways to stay afloat in troubled waters. Intelligent process automation automates tasks and transforms how QSR functions in a digital age. Following are some of the ways how IPA is transforming the QSR industry
• AI-enabled systems personalize customer experience by analyzing past orders and preferences, predicting future orders, and suggesting meals. It leads to faster and more efficient customer service.
• RPA reduces staff workload by automating routine tasks like billing, order taking, and addressing customer queries. Employees can focus on other complex and user-centric tasks to improve service quality. BPM optimizes the workflows to ensure the entire operation (from kitchen to counter) runs smoothly.
• AI and BPM offer deep insights into customer behavior, operational efficiency, and sales patterns. QSRs can use this data to decide on better menu items, marketing strategies, and inventory management.
• Automating routine tasks reduces the chances of errors and upscale service delivery, leading to reduced operational costs. IPA also optimizes resource usage in the kitchen, saving money and reducing waste.
• IPA allows QSRs to adapt quickly to new market trends and customer choices. It gives QSRs the flexibility to add new menu items based on data-driven insights and deploy targeted marketing strategies to remain competitive.
Challenges and Solutions in Implementing Intelligent Automation
From the challenge of designing E2E solutions to getting the team on board with new processes, an enterprise can go through various obstacles when setting up intelligent automation. While intelligent automation has great potential for QSRs, its implementation comes with various challenges. Analyzing and implementing solutions for these challenges is key to reaping the full benefits of this technology.
Ignoring Change Management
Businesses commonly minimize or ignore change management when implementing new technology. One must plan a dedicated strategy to avoid the aftermath of this challenge. To smoothen the implementation process, engage with top-down leadership, overcommunicate with peers, and realign teams and skills to new processes. Communicate the values that intelligent automation can deliver to the teams so they can recognize maximum efficiency gains.
Initial Investment Costs
Implementing technologies like AI, RPA, and BPM could require a higher initial investment. This may range from hardware to software to system integration. Small or mid-sized QSRs may find these initial costs challenging. They can mitigate this challenge with a gradual and scalable approach during implementation. Using cloud-based services or leasing equipment can help reduce upfront costs. Calculate ROI to make informed decisions about where and how to allocate resources for maximum impact.
Low-quality and Insufficient Data
We always hear that “data is the king.” The biggest challenge in intelligent automation implementation is gaining access to high-quality and necessary data. Training AI models depends on the accuracy and preciseness of the data, which is a critical process. It requires reorganizing current processes and ensuring the security and privacy of end users.
Training and Workforce Adaption
Staff find it difficult to shift to automated systems. They fear job displacement, struggle to sync with new roles based on new tech involvement and have performance issues. This is why staff training and reassurance are crucial factors. Assure employees that new technology is an assistance tool and will not replace the human workforce. The training programs should focus on syncing teams with new technologies and help them develop skills in areas that machines cannot handle, like problem-solving and customer service.
Legacy Processes and Systems
One of the most common obstacles to implementing intelligent automation is legacy processes, talent, and systems. Business operations, IT operations, and analytics are three core areas for any business, and the best way to overcome this challenge is by having a domain-oriented and data-driven automation strategy with multiple milestones in place.
Ensuring Quality and Performance
Maintaining consistent quality and performance as automation increases could be difficult. One must have strict quality control protocols and audits to ensure consistent performance. Partnering with a professional automation QA provider can be useful in ensuring successful implementation. Using AI for continuous monitoring and predictive maintenance helps maintain service standards.
Focus on Tech-trends Instead of Results
One common mistake businesses make is focusing on implementing new technology like intelligent automation rather than the results it will give. Instead, improving end-user satisfaction or the throughput value of specific processes should be the priority, followed by aligning intelligent automation with business operations.
Summary
To survive today’s competitive environment, QSRs must integrate intelligent automation and its components to remain profitable. It can improve productivity, reduce operational costs, improve CX, and offer data-driven insights for better decision-making. AI, BPM, and RPA play a big role in improving decision-making and process automation in QSRs. These components are key in inventory management, speeding the delivery process, and reducing food wastage. Partnering with a professional test automation provider like Tx would help seamlessly adopt intelligent automation.
How can Tx help with Intelligent Automation Implementation?
Implementing intelligent automation in the QSR industry involves a range of complex challenges associated with integrating advanced technologies such as AI, ML, and RPA into existing systems. These technologies are crucial for enhancing service speed, order accuracy, and overall customer satisfaction but require rigorous testing and fine-tuning to align with operational goals and achieve the desired results.
Given the complexities of intelligent automation architecture, partnering with a reliable and experienced test automation service provider is crucial. Tx, with its deep expertise in automation, AI, ML, and RPA, can assist you in implementing intelligent automation in your QSR operations. Our strategy includes selecting the right tools and frameworks, defining business goals, and running tests early and frequently to detect and resolve issues efficiently. Following are some of the reasons to partner with Tx for upscaling your QSR initiatives with intelligent automation:
• We manage the entire test cycle to ensure efficient execution and seamless integration of intelligent automation technologies in QSRs.
• Our advisory services are designed to maximize efficiency in the automation process. For QSRs, this means identifying and minimizing risks associated with integrating new technologies and ensuring a solid return on investment, which is vital for the industry’s cost-sensitive nature.
• As an extended QA arm within the Total Center of Excellence (TCoE), Tx can closely collaborate with QSR teams to ensure the high performance and reliability of QSR automation systems.
• Our tools and technology-agnostic frameworks, like Tx-Automate, Tx-QSR, and Tx-HyperAutomate, seamlessly integrate with the existing automation frameworks and save scripting effort and cost.
To know more, contact our QA experts now.
Discover more
Stay Updated
Subscribe for more info